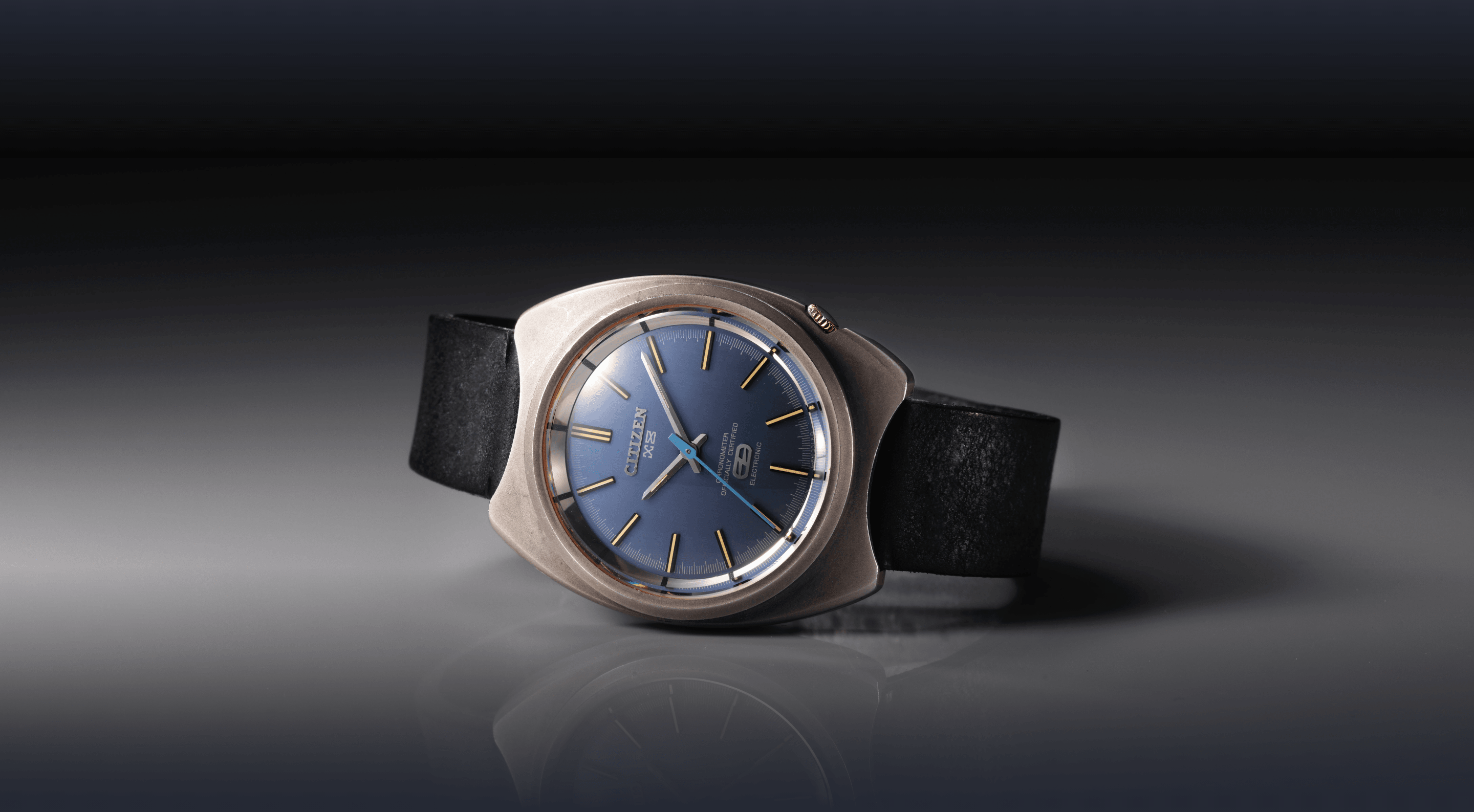
CITIZEN and Titanium:
A Journey
“Challenge.” “Technique.” “Gentleness.” “Strength.” “Space.” “Colour.”
Explore CITIZEN’s titanium technologies through six themes.
Challenge
In a single-minded search for the ideal material for watches, CITIZEN chose to set its sights on titanium, a material with infinite possibilities. After extensive research and development, CITIZEN released the world’s first titanium watch, the X-8 CHRONOMETER, in 1970. The long challenge to get the most out of titanium had begun.
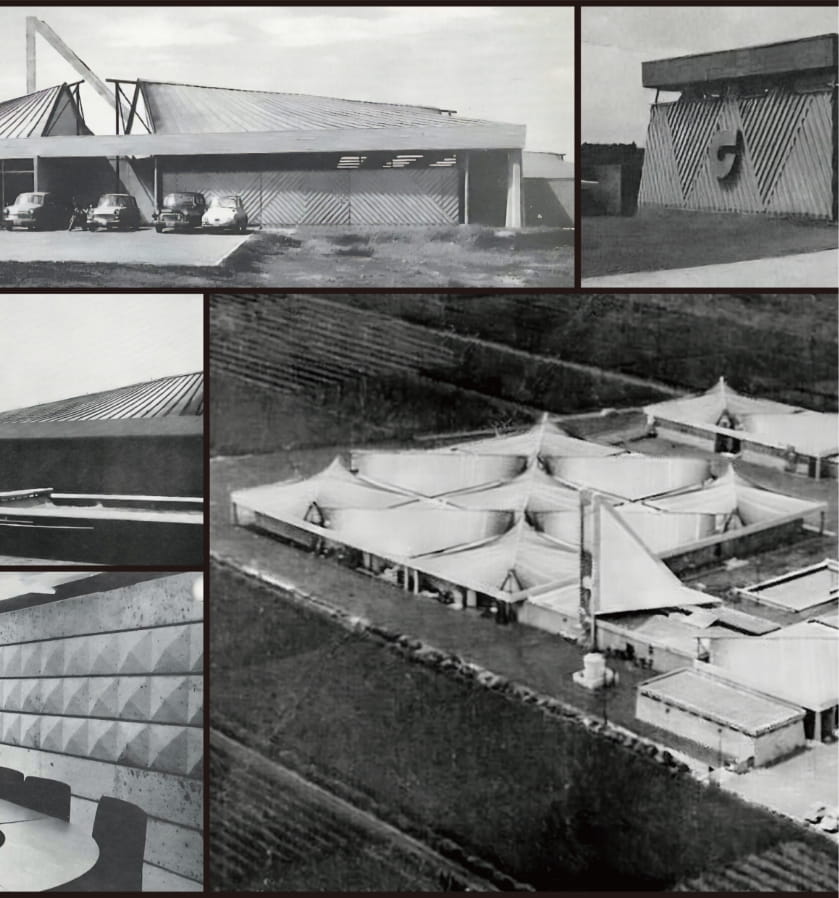
The AT Strategy
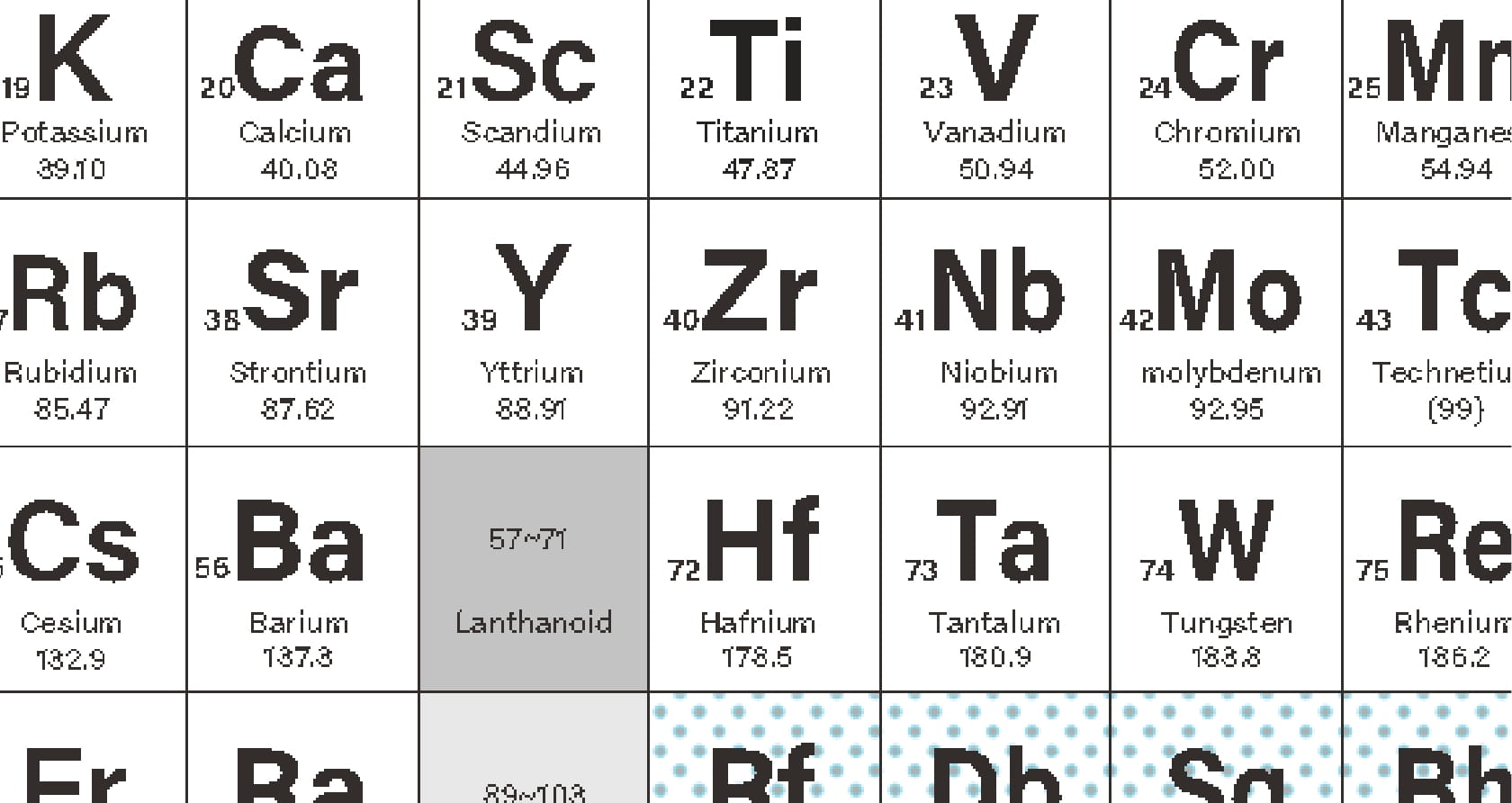
Titanium,
Element No. 22
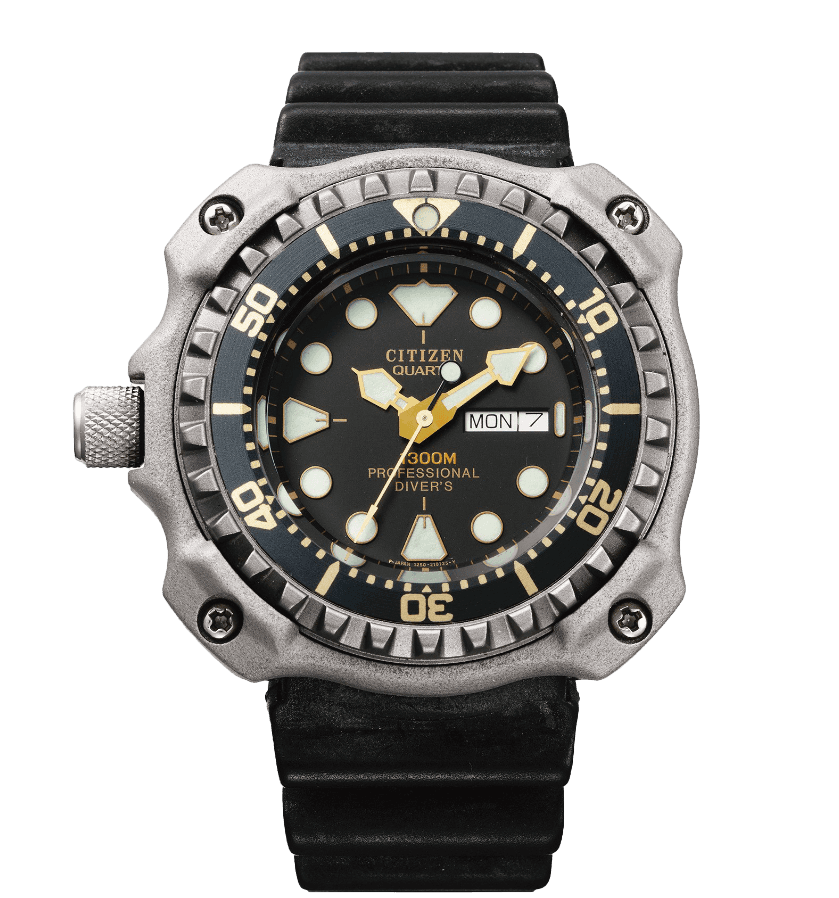
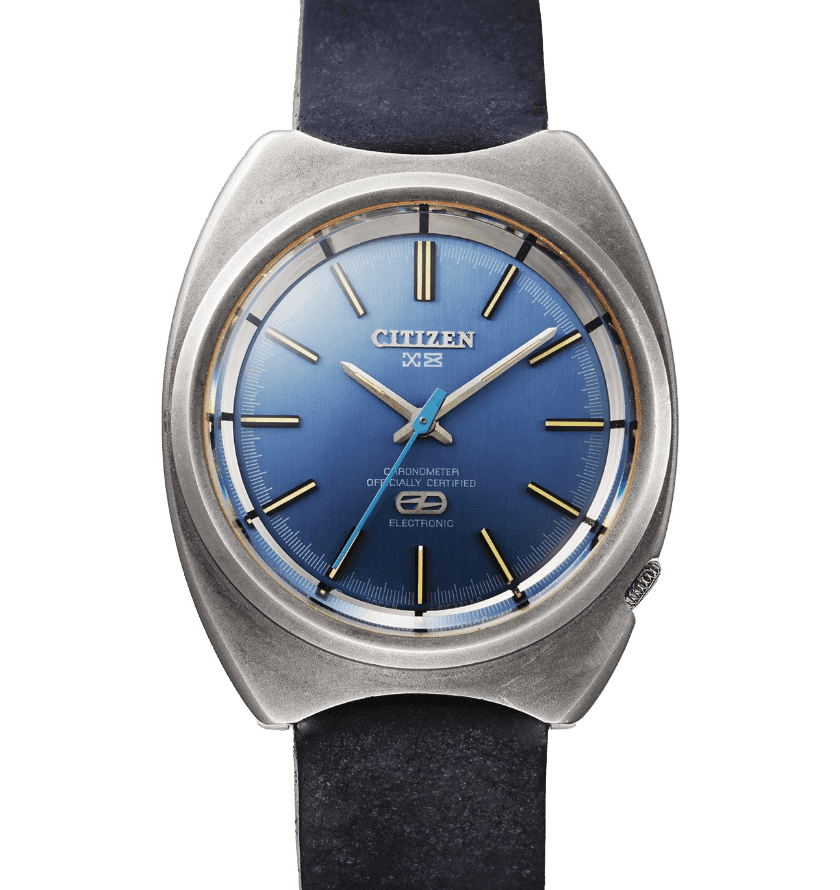
Technique
Titanium is an extremely difficult metal to process. Back in the early days, CITIZEN engineers nicknamed titanium “triple trouble” because it could not be pressed, machined or polished. Among the challenges it presents are low thermal conductivity, a tendency to stick to the machining edges of cutting tools, and highly combustible shavings. The impossibility of achieving a mirror finish regardless of how long it was polished was an additional challenge. By devising ingenious techniques to solve all these problems, CITIZEN invented processing technologies that were beyond the capabilities of any other company at the time.
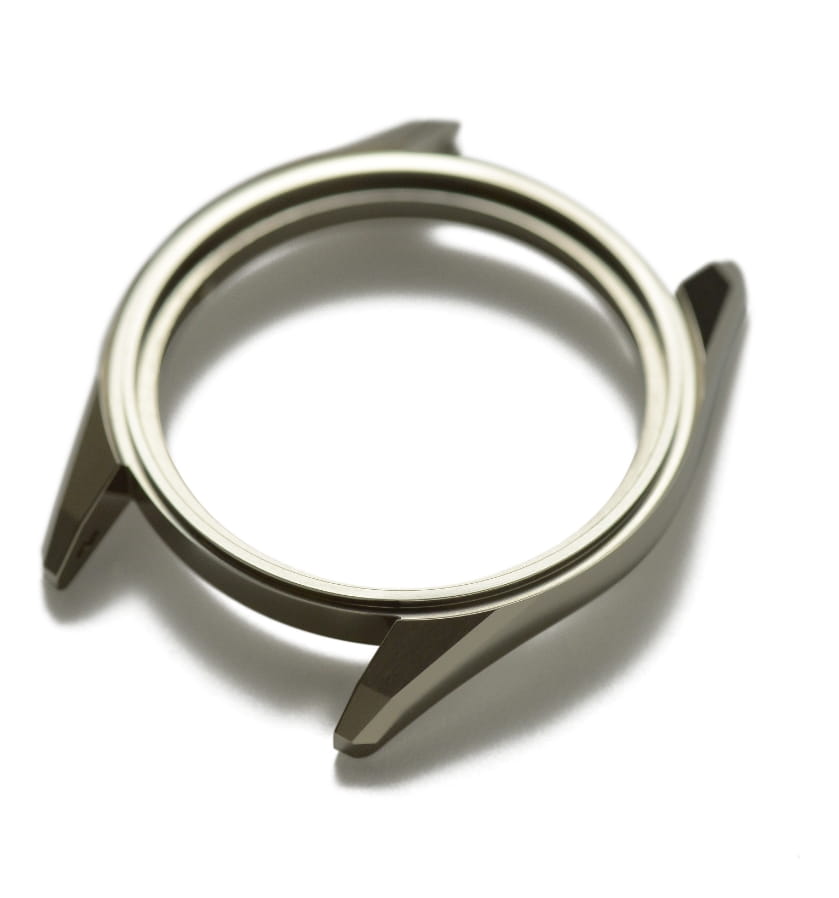
Case Manufacturing Process
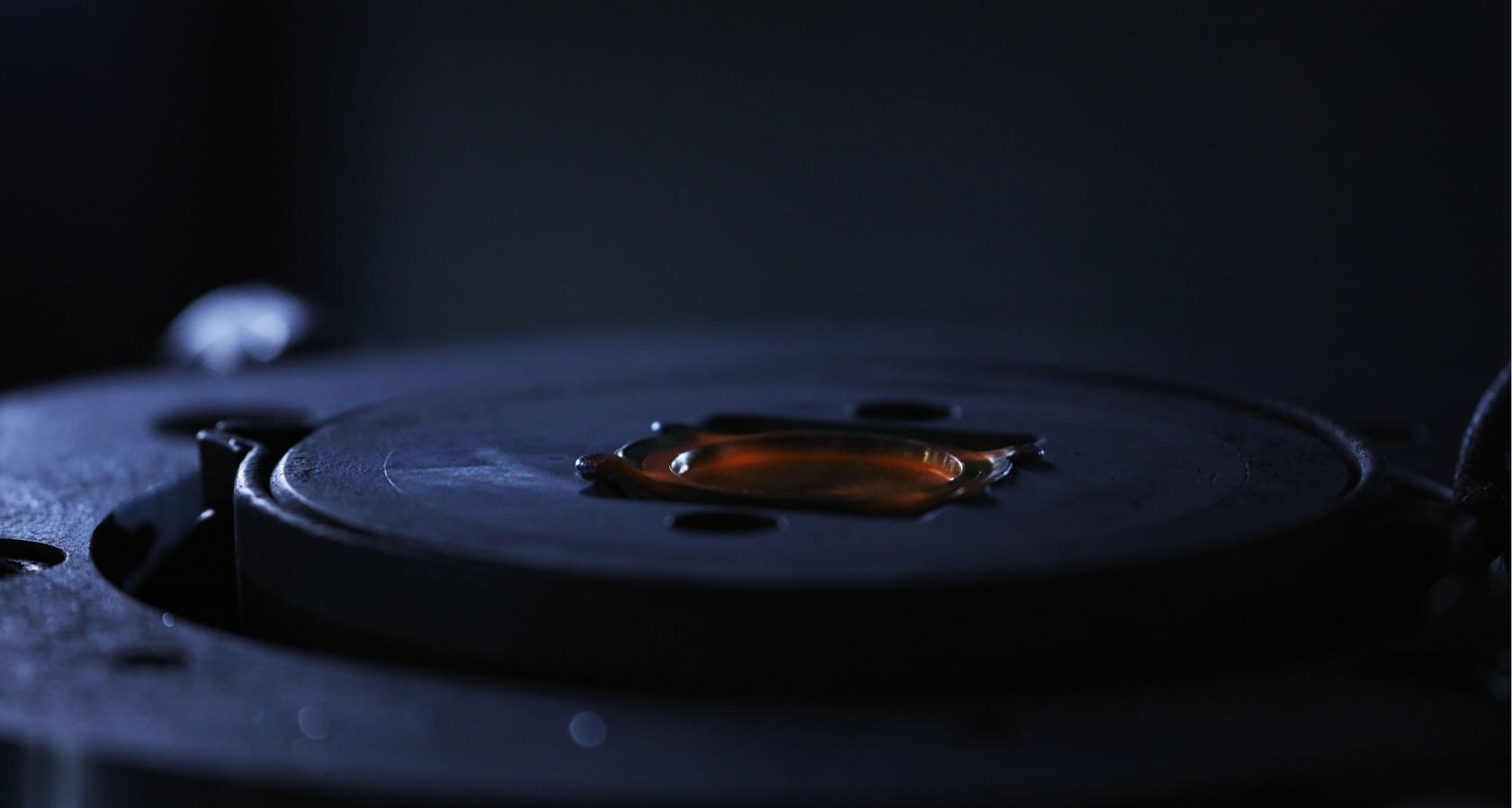
Hot Forging
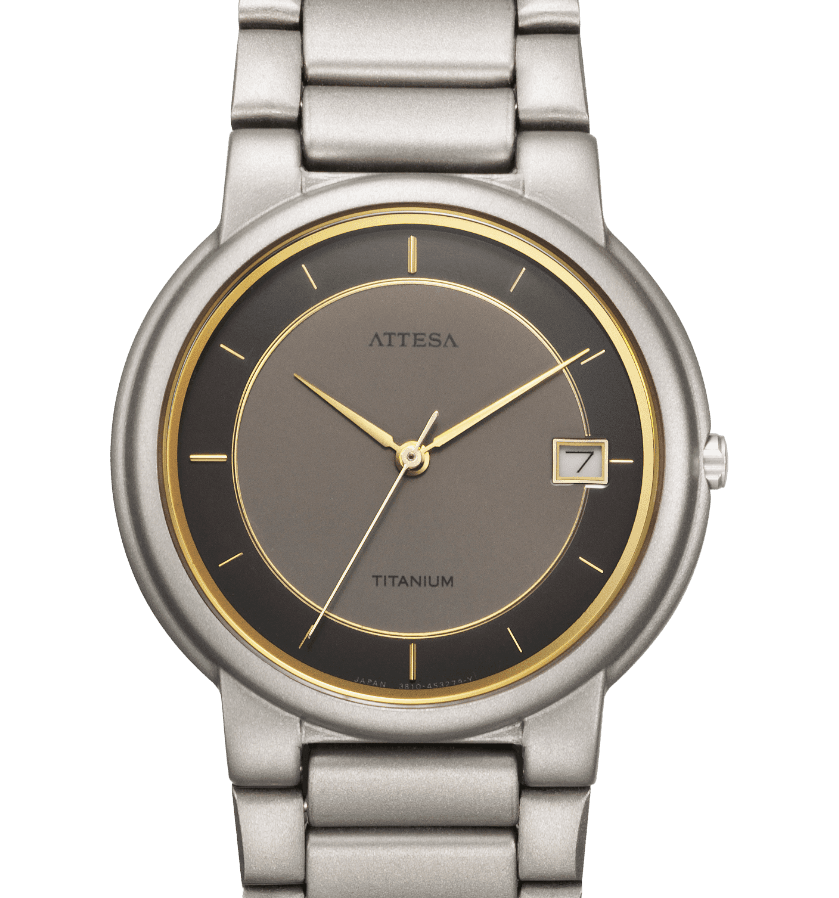
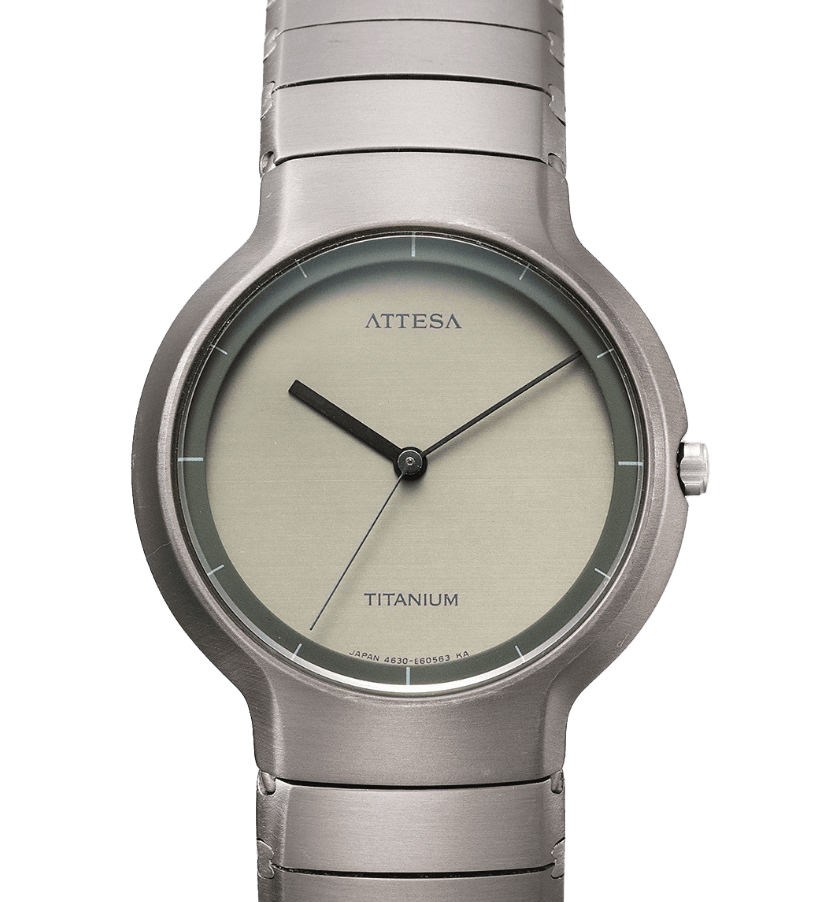
Gentleness
Seeking to establish the optimum relationship between the environment, people and their watches has been a CITIZEN leitmotif for decades. We want to create watches that minimise physical or mental stress, enabling people to use them in comfort and with peace of mind, while also deploying environment-friendly materials and manufacturing processes. This was the thinking that propelled the advance of CITIZEN’s titanium technologies.
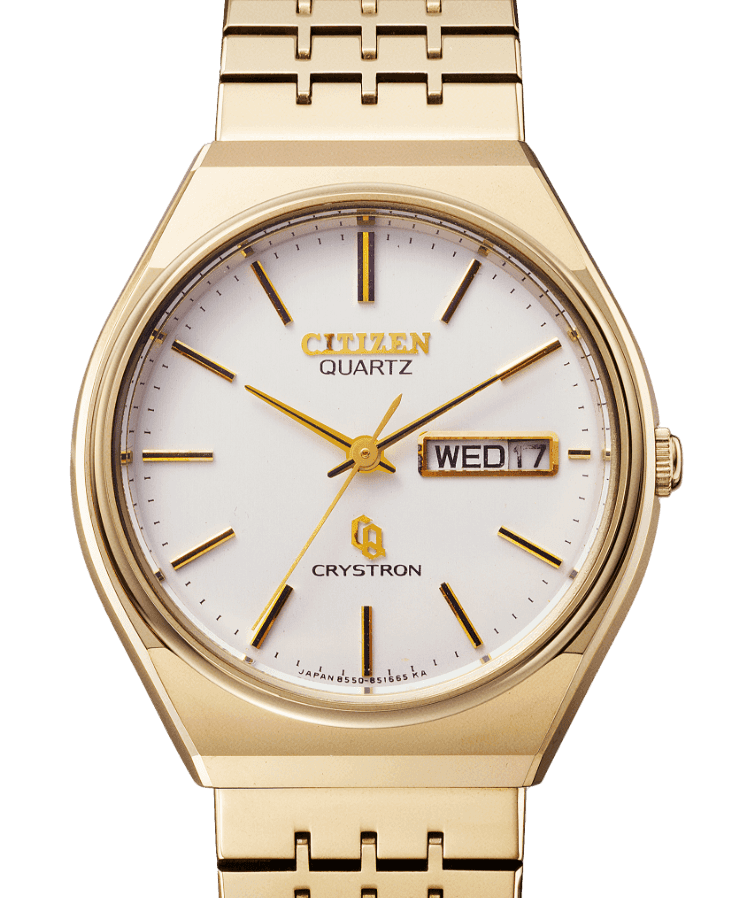
From Wet Plating
to Dry Plating
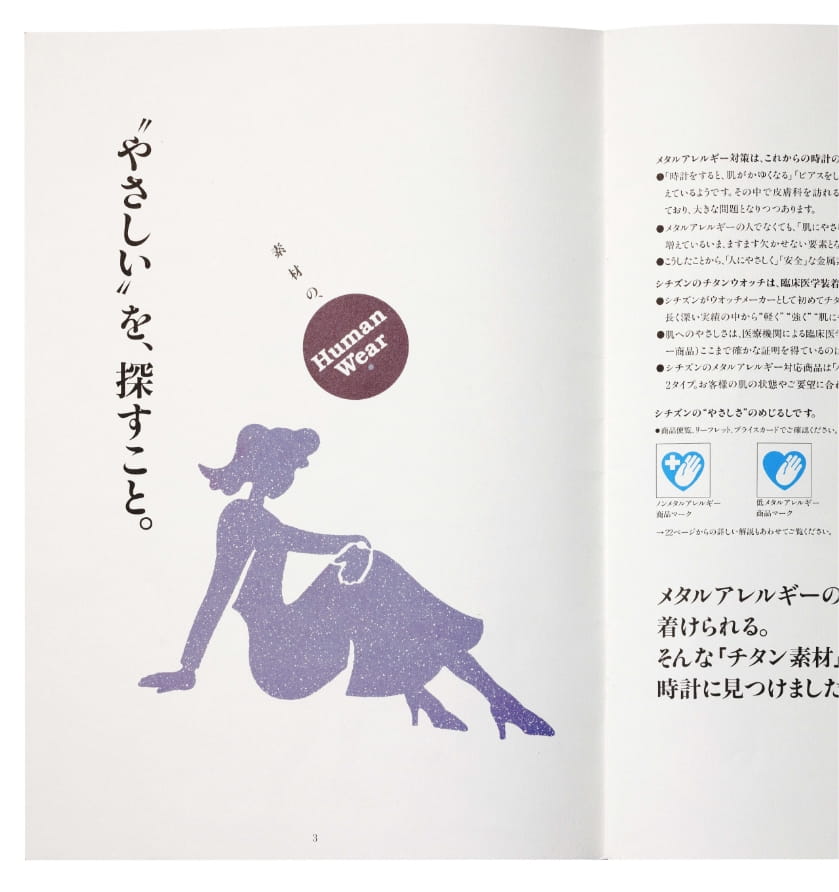
Human
Wear
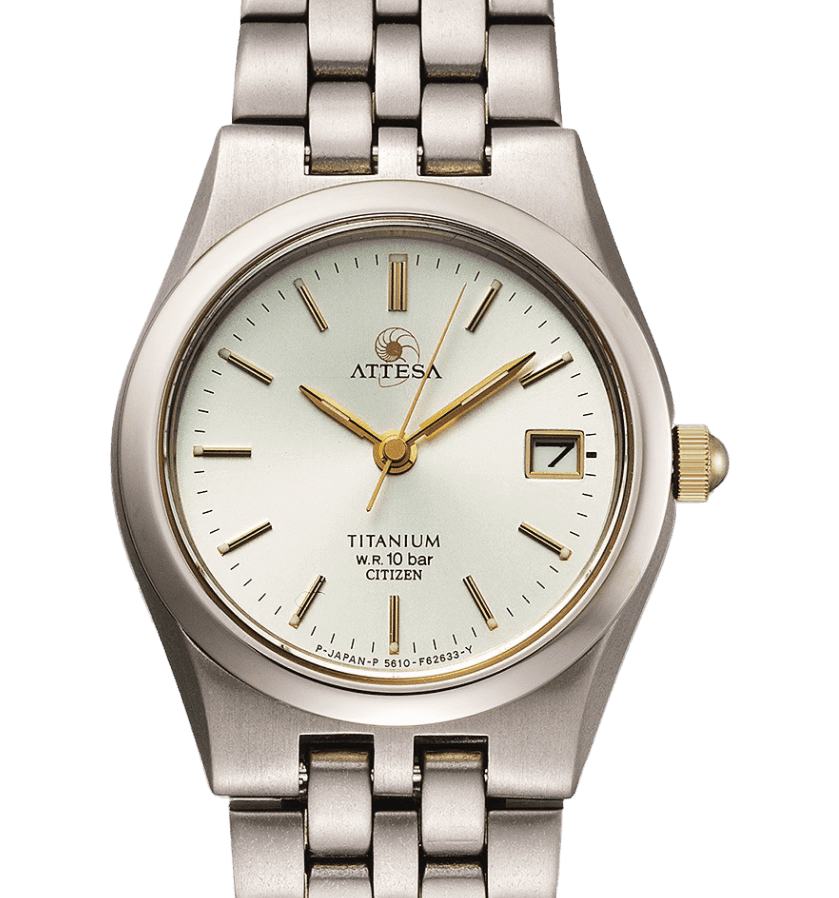
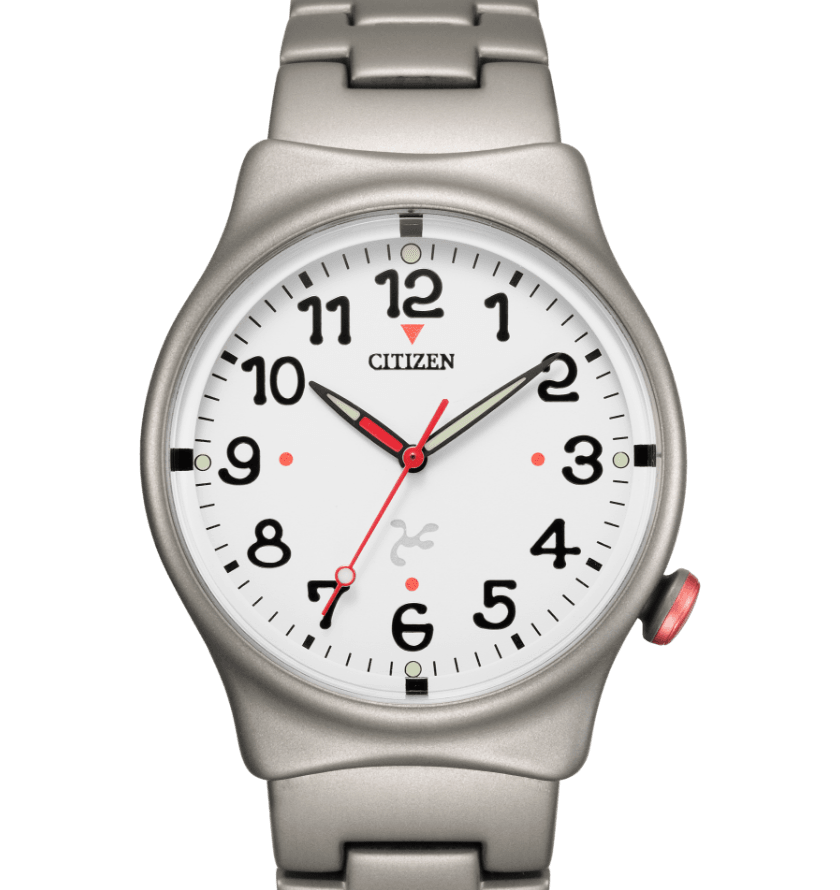
Strength
At CITIZEN, we want people to enjoy the time they spend with their watches and to love their watches more, the longer they use them. That thinking prompted us to ask how we could overcome one of titanium’s downsides—namely its scratch proneness. After many years of experimentation, the solution we finally arrived at was DURATECT, our proprietary surface-hardening technology, which achieves a dramatic improvement in surface hardness while also preserving the watch’s pristine appearance. Of benefit to anyone who truly loves their watch, the functional strength of DURATECT plays a crucial supporting role in Super Titanium™.

10-year Scratch Comparison Test Samples
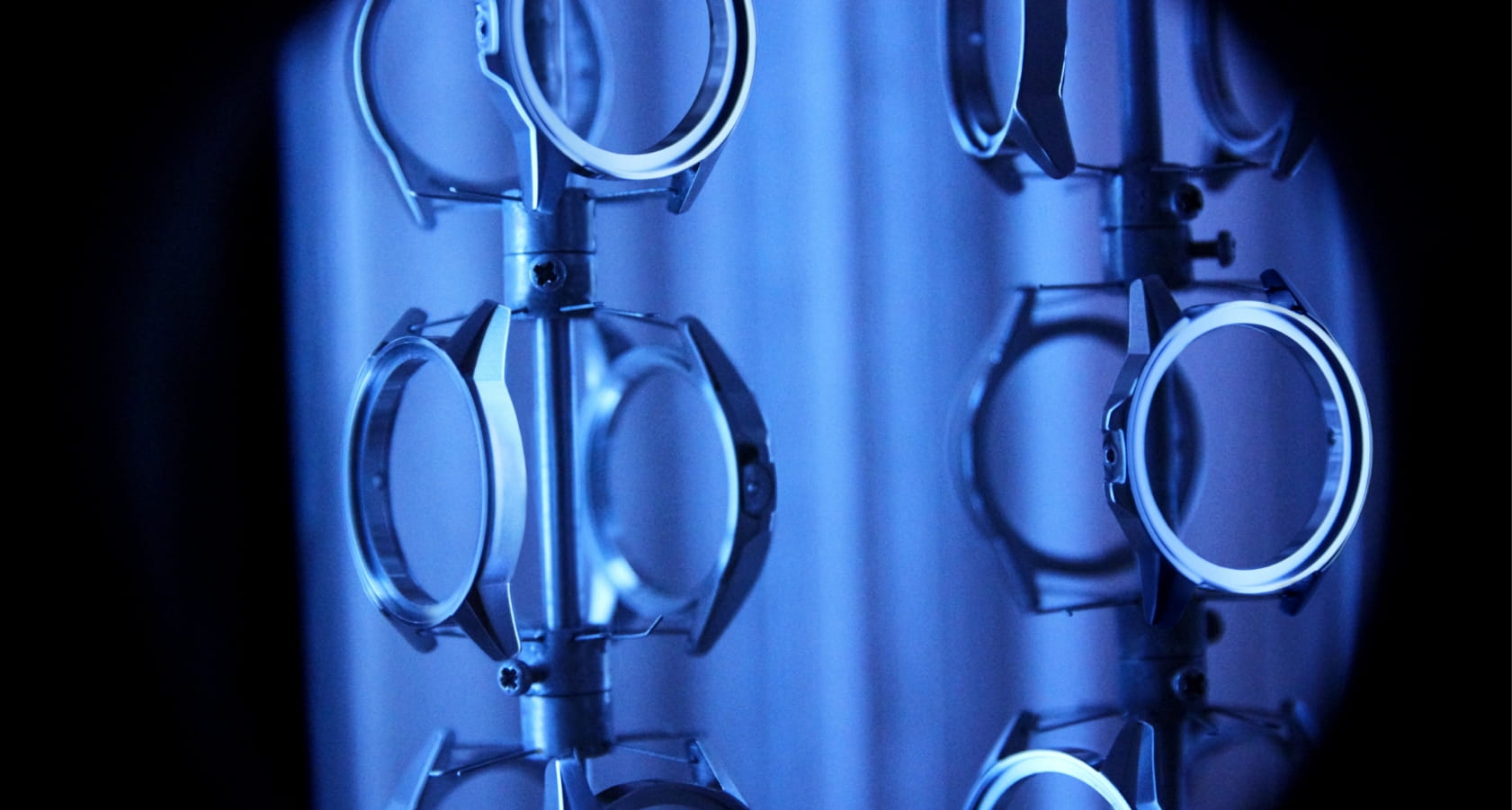
Surface Hardening
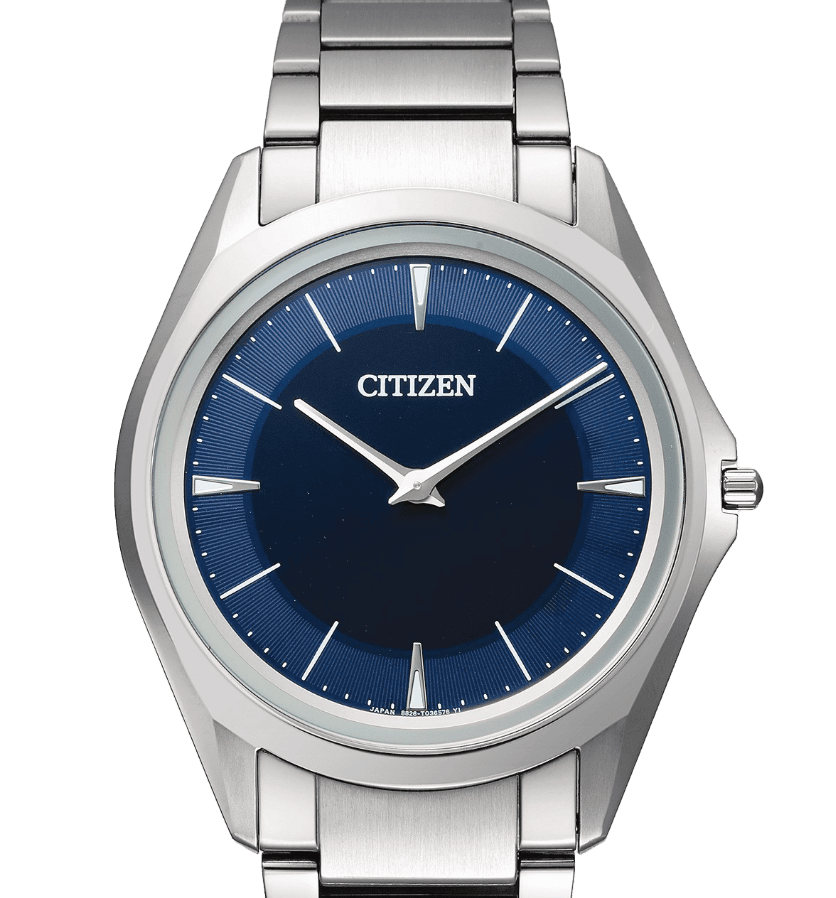
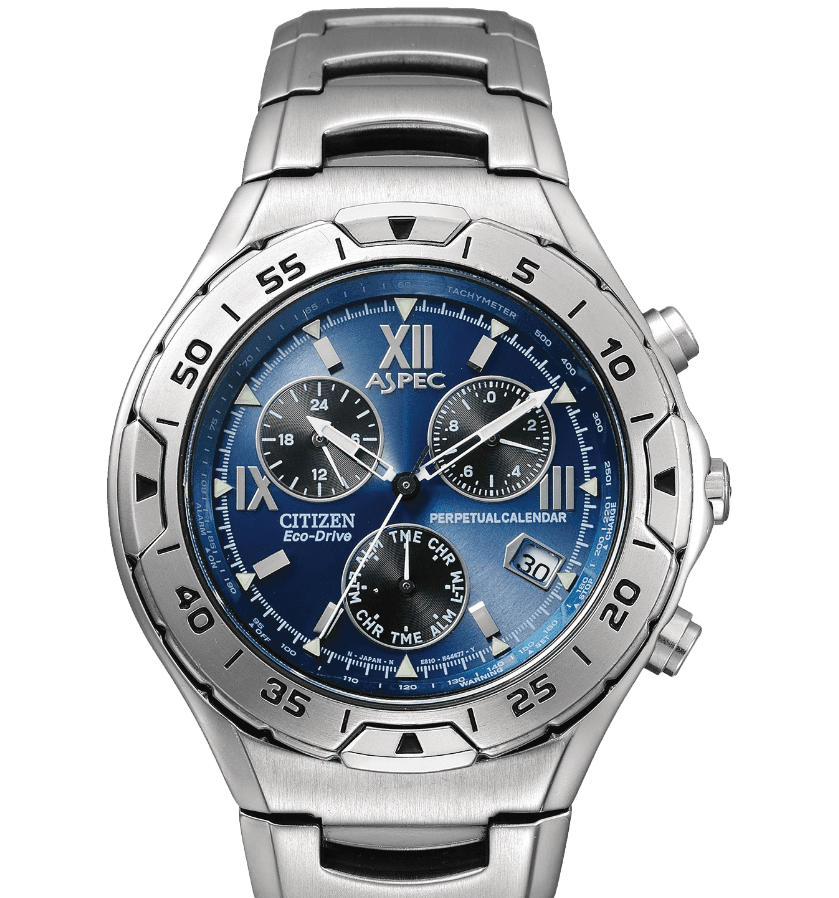
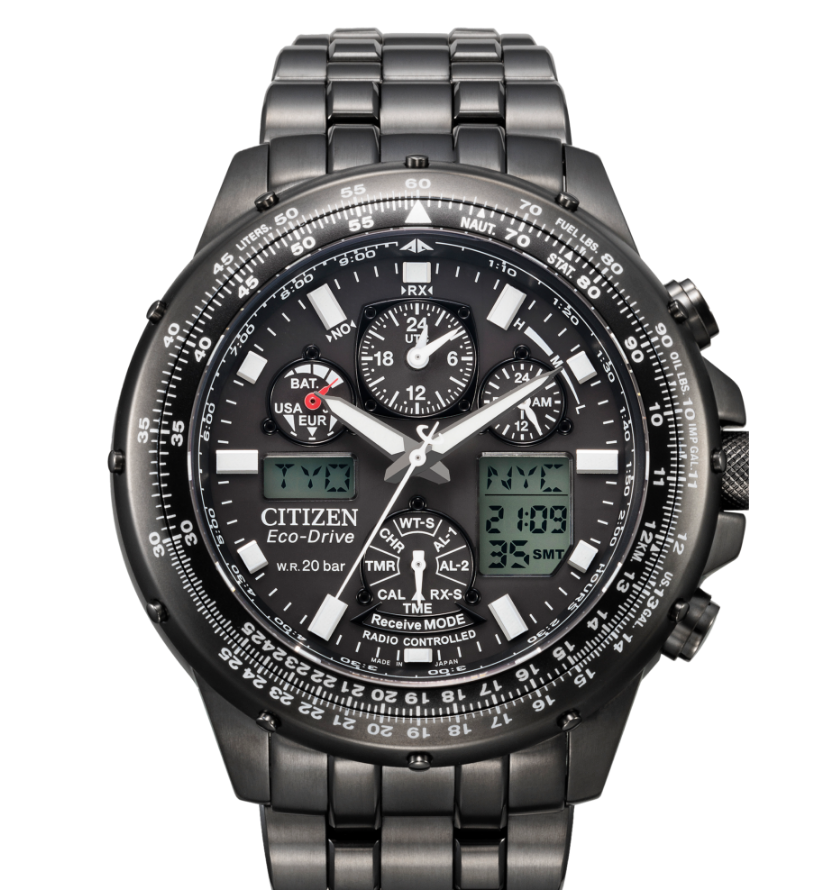
Space
“Let’s make a watch with a space-age material.” It is the 1960s and the whole world is fixated on the Apollo Program, the first manned mission to the moon. Because of its lightness, strength and corrosion resistance, titanium is attracting attention as a material well suited to space. “In addition to being light and corrosion resistant, titanium also guards against metal allergy. Doesn’t that make it the perfect material for watches that people wear directly against their skin?” This was the insight that served as the starting point for CITIZEN’s research into titanium.
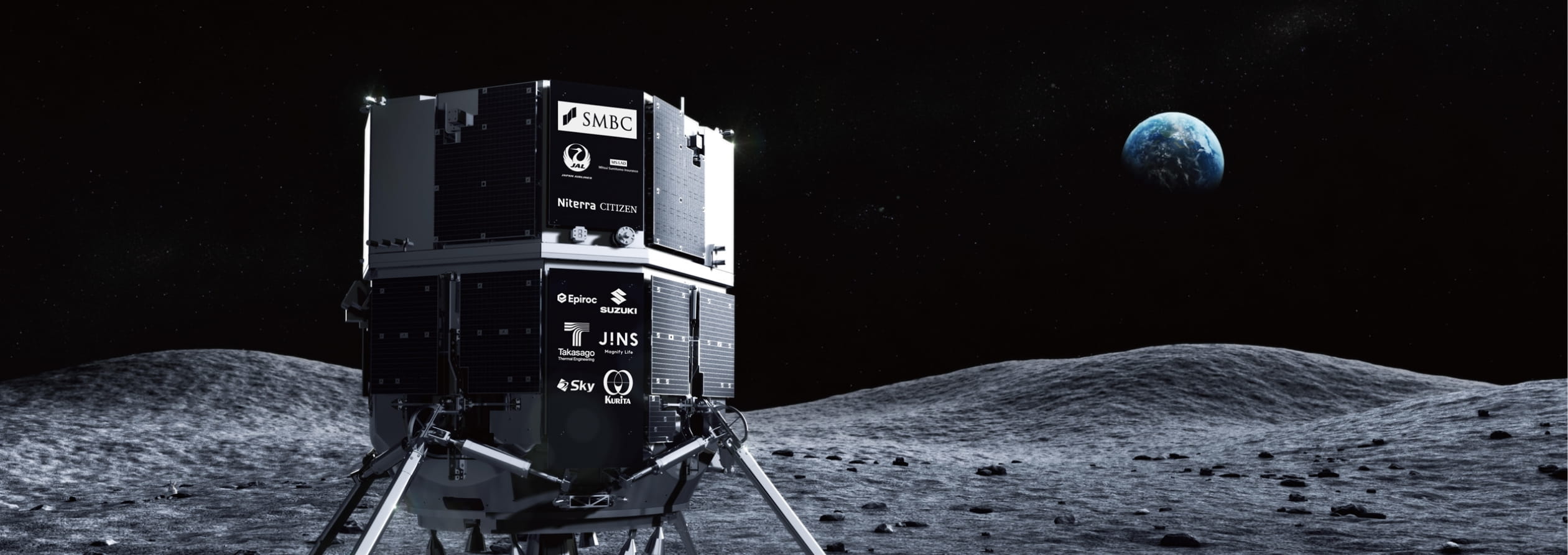
HAKUTO-R
Programme
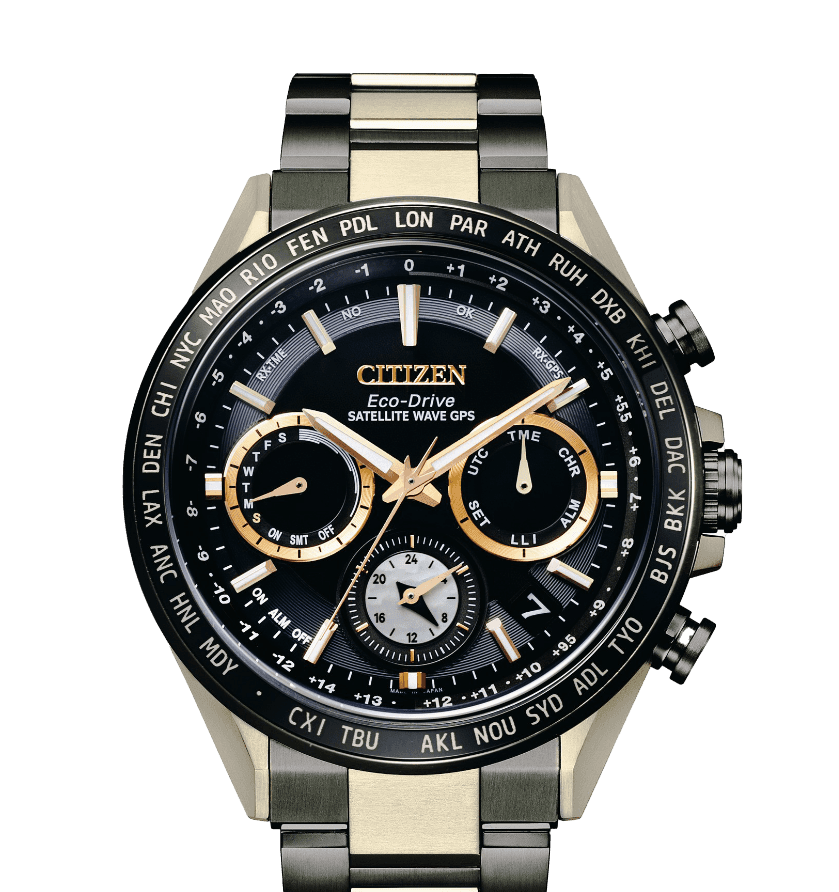
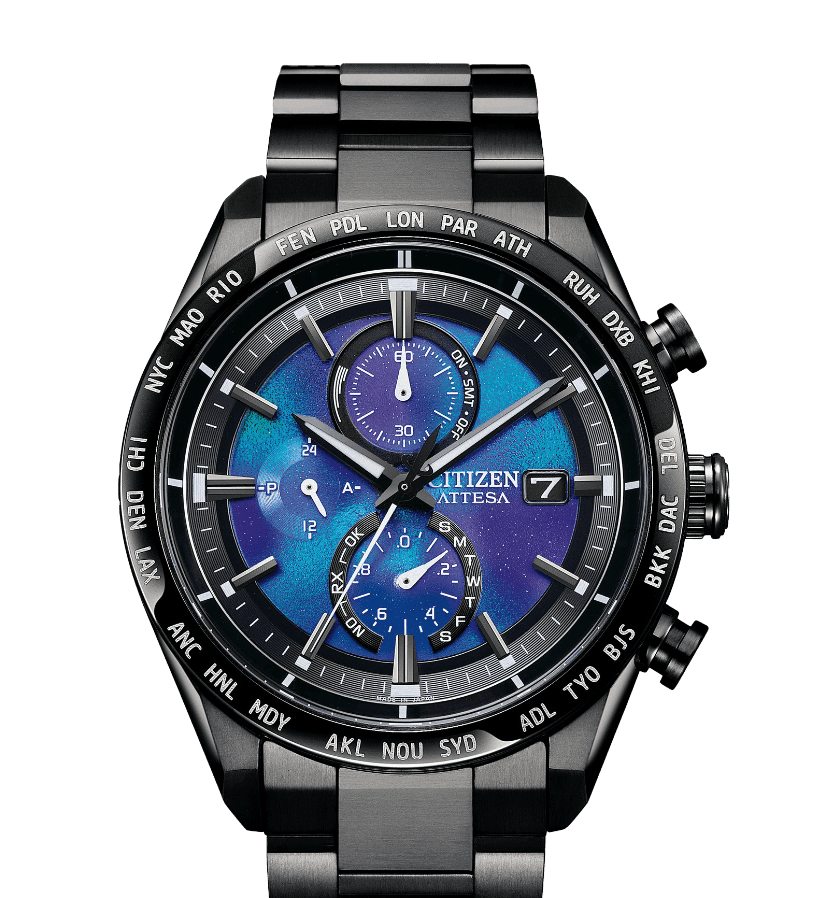
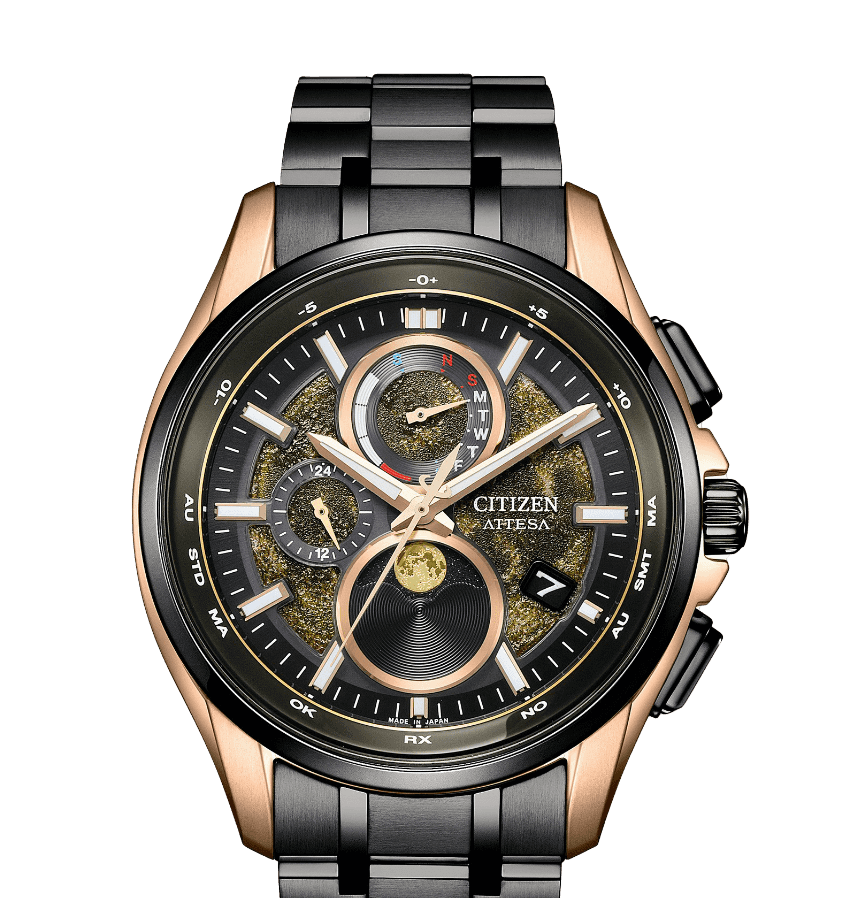
Colour
A watch is at once a precision instrument and an accessory that serves to accentuate the individual character of the wearer. Originally developed to protect the pristine beauty of watches, DURATECT has evolved in response to user needs and now comes in a range of beautiful colours.

Colour Variations
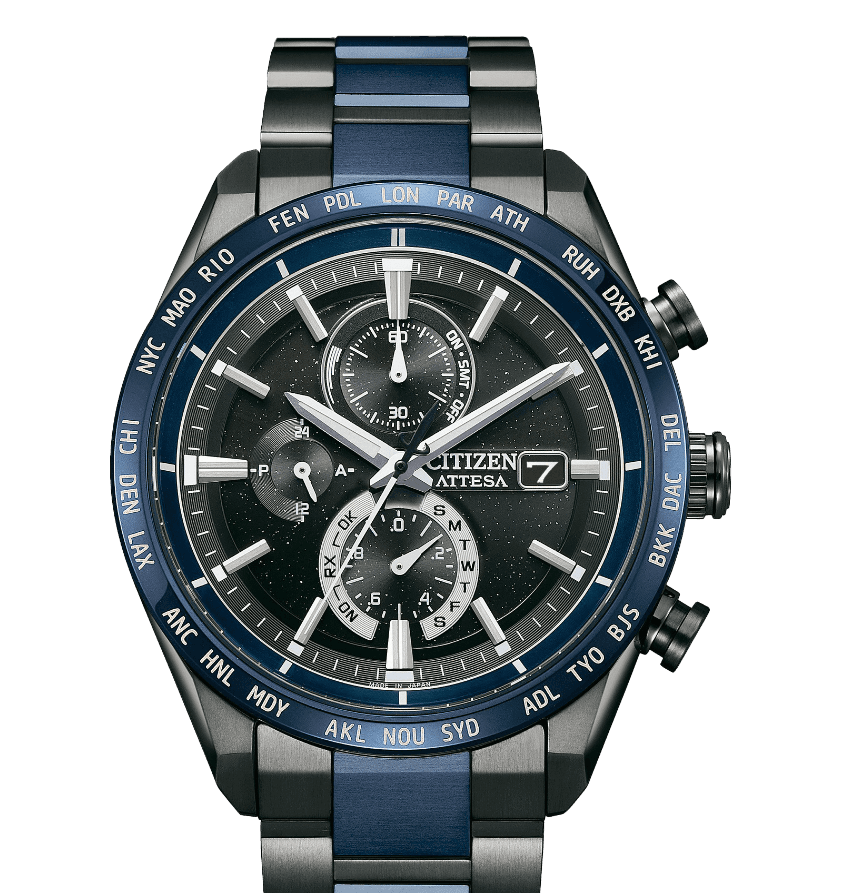
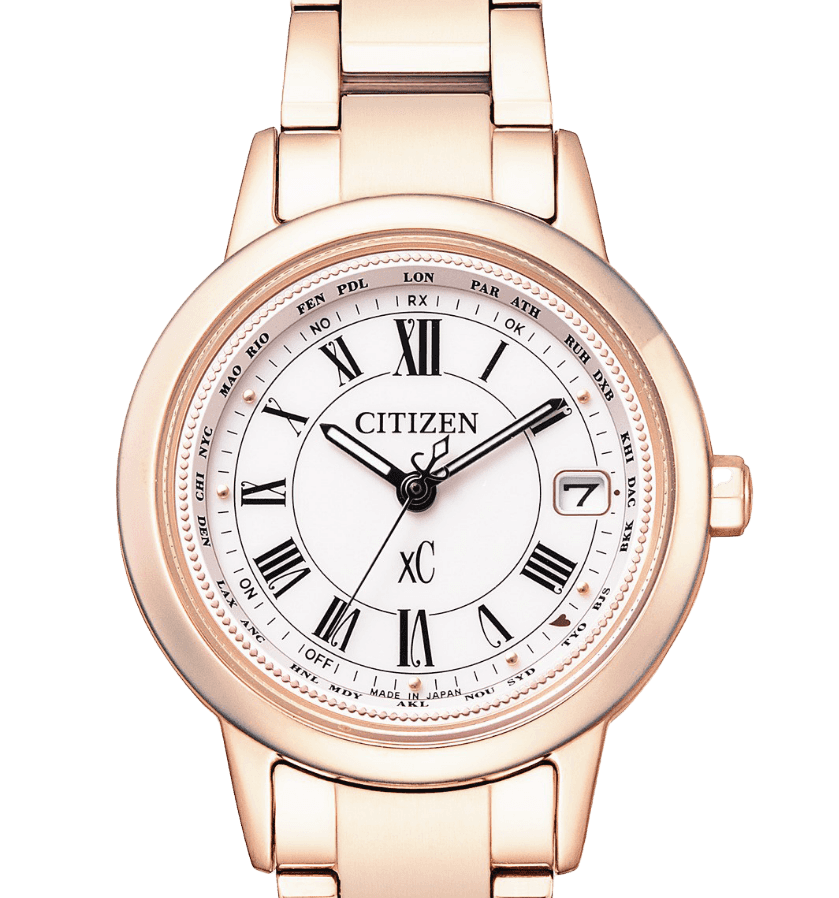
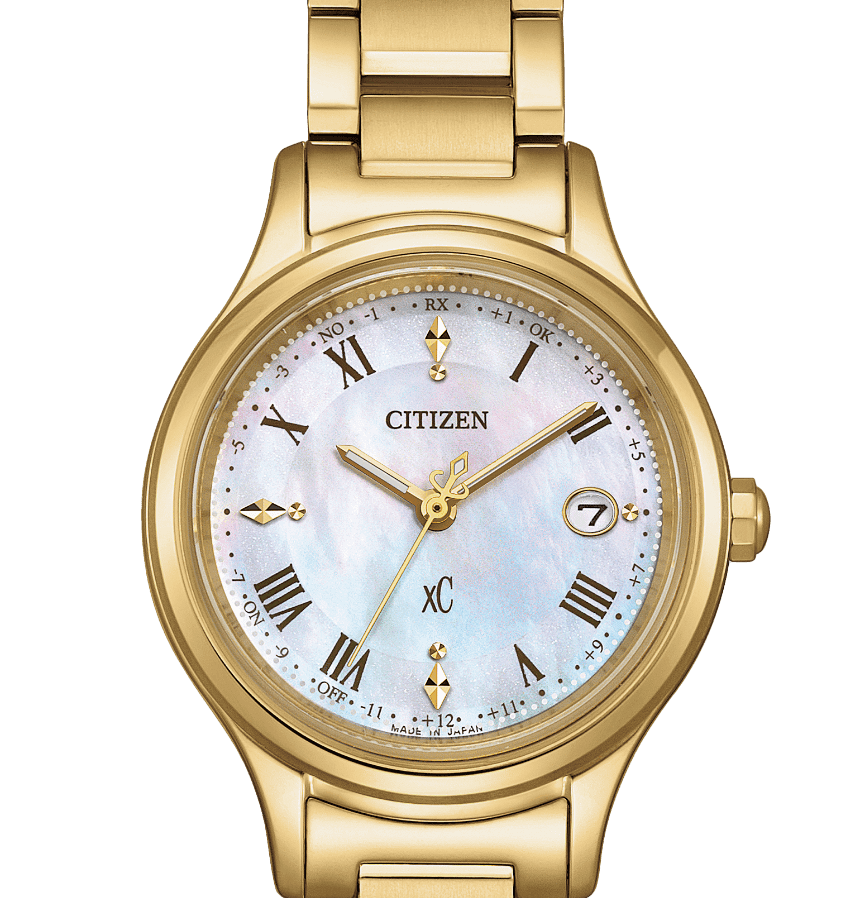
The AT Strategy
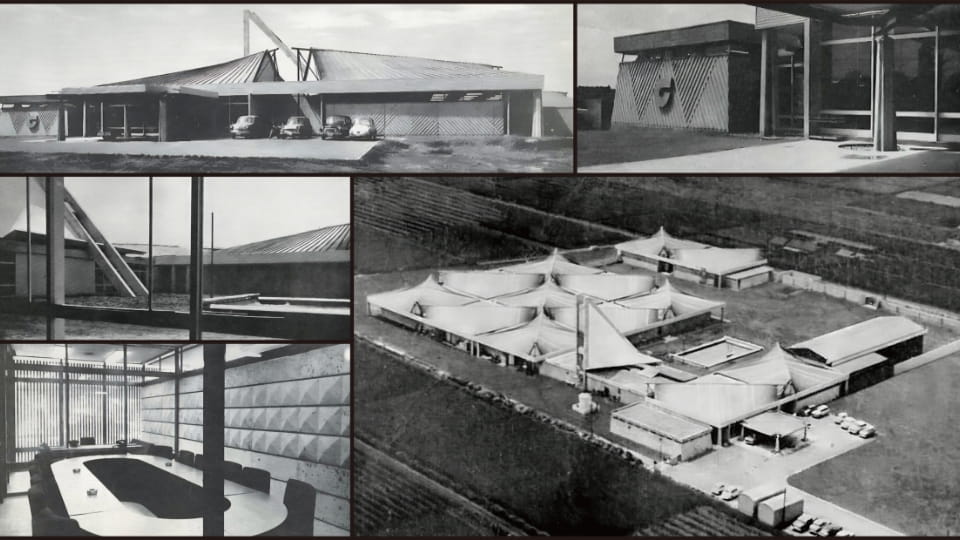
Technology research laboratory
Around 1970, traditional materials like stainless steel and brass were only able to express a limited range of colours, so the need to develop a new material capable of responding to changing fashion trends was very real. CITIZEN initiated an intense research programme focused on aluminium and titanium. At this point, hard anodised aluminium technology was still at the research stage. Moreover, it was very difficult to mass produce small products like watches with a uniform coating. That is why CITIZEN opted to explore titanium exteriors as a parallel development theme. It was around this time that robust collaboration between CITIZEN engineers and designers really took hold. The AT Strategy progressed in strict secrecy, taking its project name from the first letters of the two chemical elements’ symbols, the A (of Al) and T (of Ti).
Titanium, Element No. 22
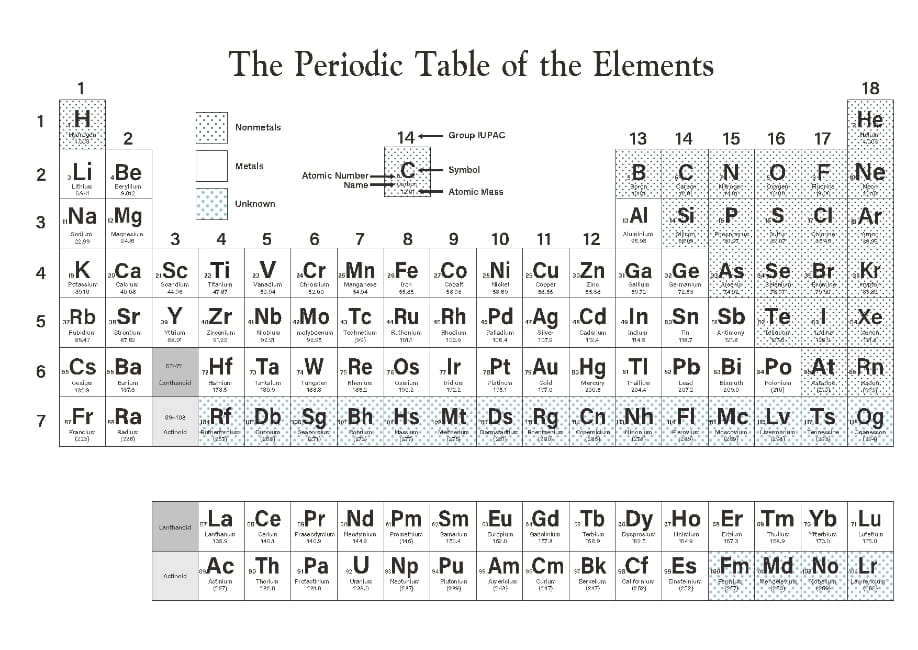
First discovered at the end of the eighteenth century, titanium is a comparatively young metal. Its name comes from the Titans, the older gods of Greek mythology. High-purity titanium was first successfully isolated in the United States in 1910. It was in the 1940s that the production of titanium as a raw material and commercial production got underway in earnest with a view to industrial use. The appeal of titanium as a metal lies in its lightness, corrosion resistance, heat resistance and biocompatibility.
Case Manufacturing Process
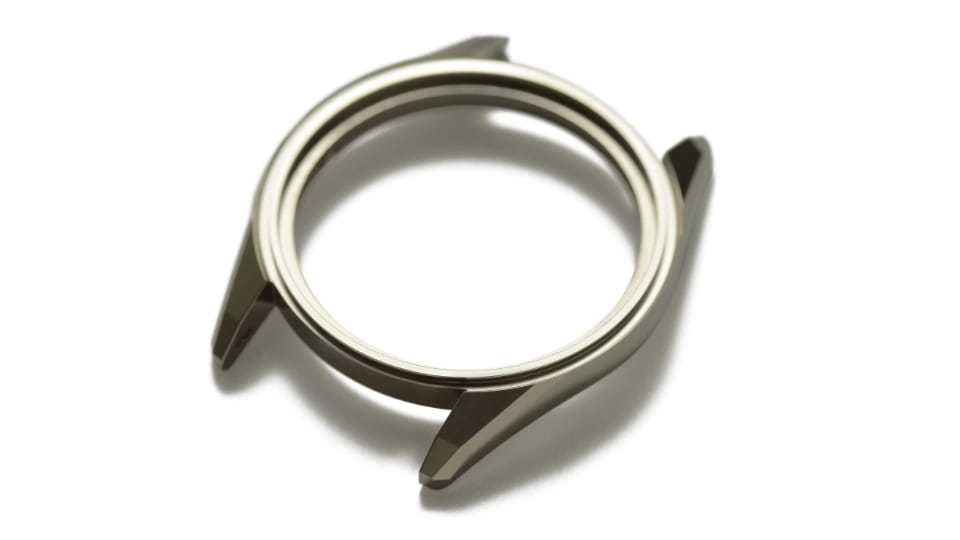
Because titanium is a difficult metal to handle, processing it into a meticulously crafted product requires an extremely high level of technology. At CITIZEN, we have spent many years researching titanium and developing special processing technologies for it. In addition to our obsessive attention to the material itself, we have achieved beautiful finishes through precise pressing, machining and polishing. A single round of processing, however, is not enough to make the finished watch case. It is only by repeated processing that the case attains its final shape.
Hot Forging
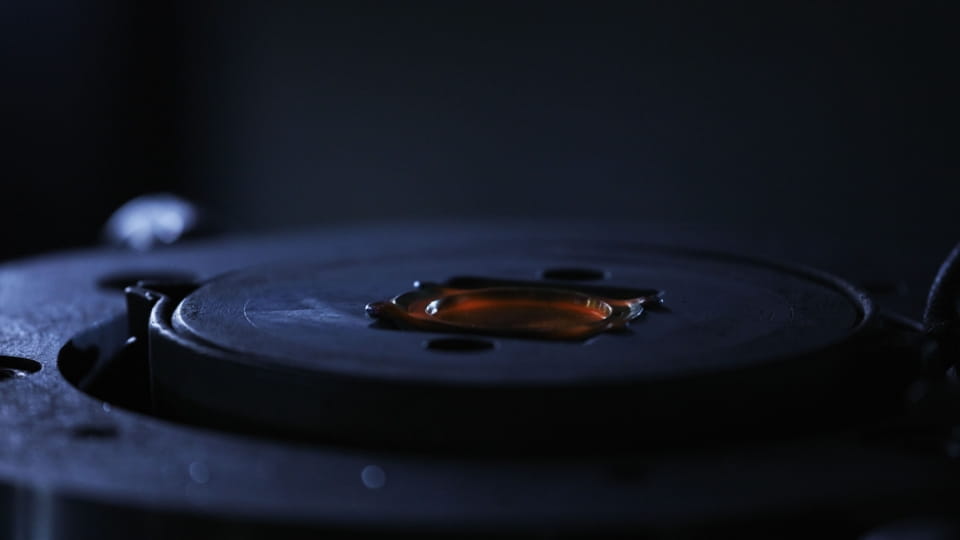
In the pressing process, a shape is transferred to the titanium through hot forging. Temperature management and die-release technology play a key role here. Heating titanium to a high temperature reduces its deformation resistance and makes it possible to press-form it into a variety of shapes. Any excess metal is sliced off to prevent titanium chips from sticking to the die. Despite titanium’s reputation of being stubborn and sticky, the cut is a clean one.
From Wet Plating to Dry Plating
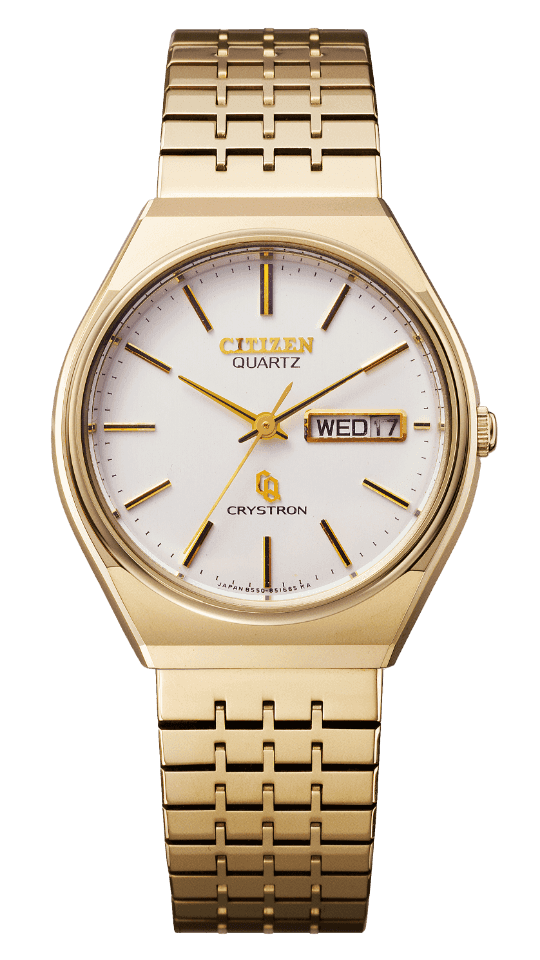
Model no longer available
As pollution became an ever more salient issue in the late 1960s, expectations rose for a new plating technology that would take the place of wet plating and do away with liquid-based processing. In 1974, CITIZEN was one of the entities that started developing multi-cathode-style ionisation plating technology in response to an appeal from the Research Development Corporation of Japan (now the Japan Science and Technology Agency). We designed innovative in-line ion-plating equipment, releasing Mirador, an exterior treatment based on this new plating technology, in 1977. In 1981, CITIZEN won the Inoue Harushige Prize in recognition of our contribution to the development and practical application of dry plating. Our continued development of related technologies culminated in today’s DURATECT which plays such a crucial supporting role in Super Titanium™.
Human Wear
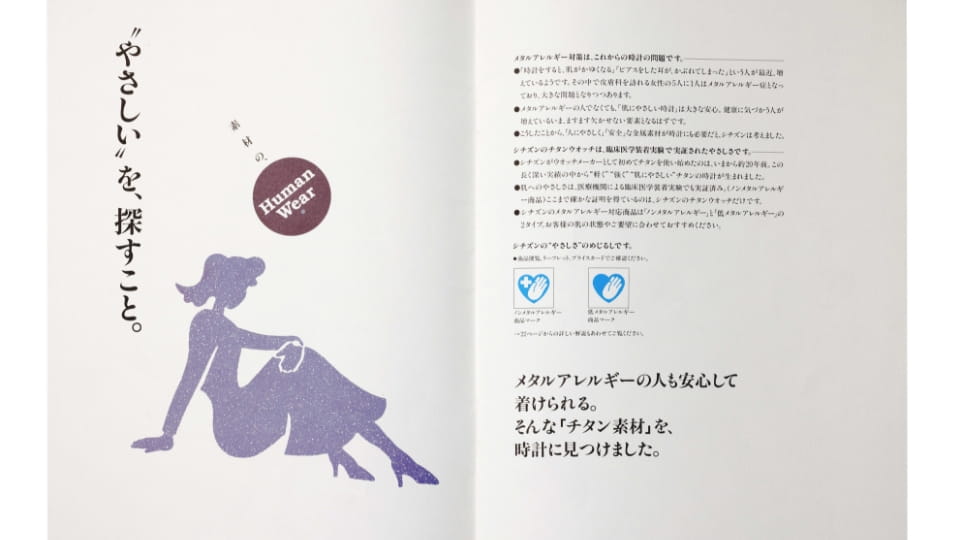
The CITIZEN “Human Wear” philosophy of watchmaking took shape around 1990. It was a development philosophy that sought to meld human-friendly design with environment-friendly manufacturing practices. Tackling metal allergy was one area that CITIZEN addressed with vigour. Our titanium watches that coupled a beautiful finish with minimal use of allergy-triggering metals generated very warm consumer feedback. Clinical trials conducted with the guidance of a team of dermatologists proved that the watches were indeed safe to wear. The “Human Wear” philosophy of “kindness to people” and “user-friendliness” still underpins CITIZEN’s watchmaking today.
10-year Scratch Comparison Test Samples
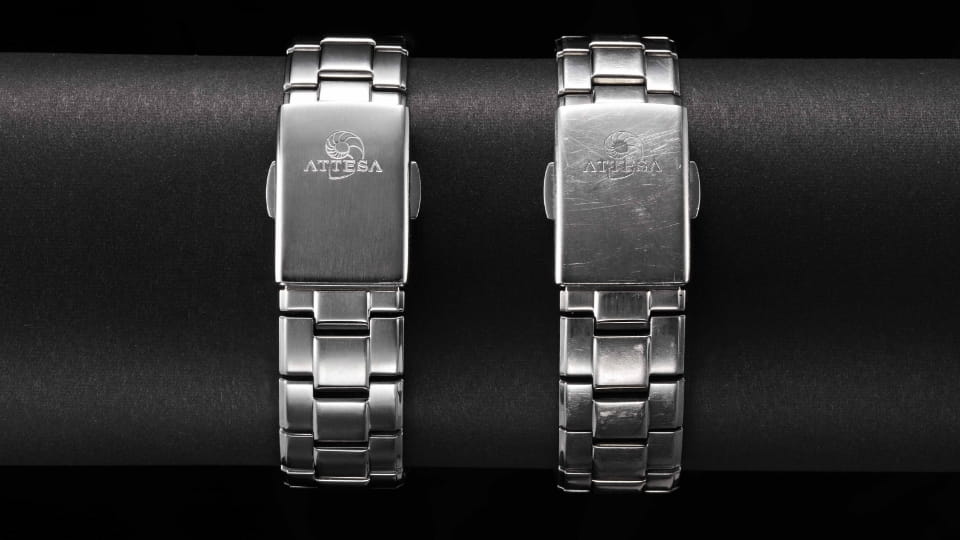
Left: Super Titanium™ watch
Right: Watch of untreated titanium
A watch that is going to be used for any length of time must be durable and keep looking good. In order to show that Super Titanium™ is genuinely scratch resistant in real-life environments, one CITIZEN engineer wore a Super Titanium™ watch treated with DURATECT while another wore an untreated titanium watch. The observational study covered a 10-year stretch. A comparison of the Super Titanium™ watch vis-à-vis the untreated titanium watch confirms the outstanding durability of the former.
Surface Hardening
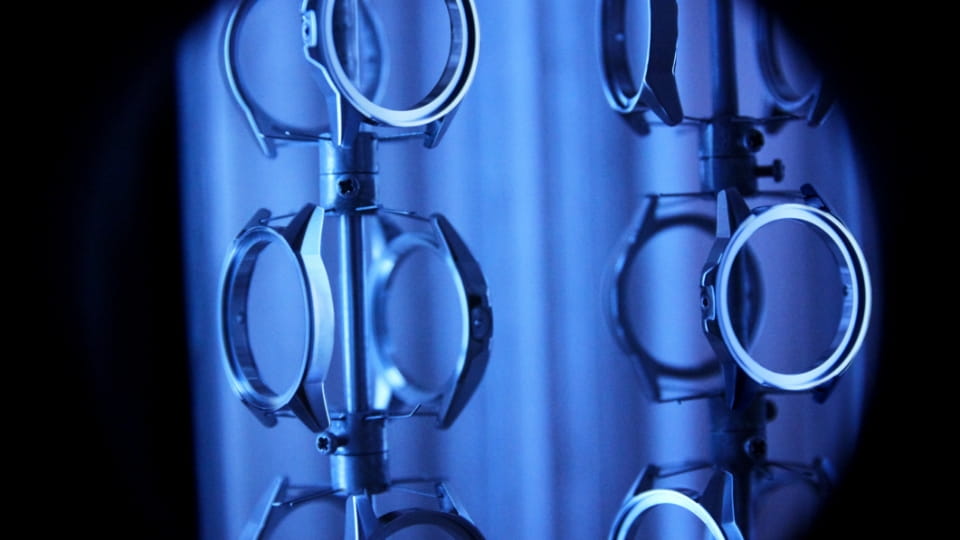
The acceptance inspection of watch components like the bracelet and case is the first stage in the DURATECT treatment process. That is followed by cleaning and the cleaning inspection; then film deposition and the film deposition inspection; and finally packing and shipping. Meticulous before-and-after checks of the components are conducted at every stage. The fact that these inspections are carried out by the human eye guarantees high quality. When it comes to applying a beautiful coating efficiently and consistently to all the components, the design and placement of the jigs is crucial. Careful daily maintenance is required, up to and including keeping the insides of machinery and equipment clean and tidy. This thoroughgoing quality management regime is what sustains the high quality level of DURATECT.
HAKUTO-R
Programme
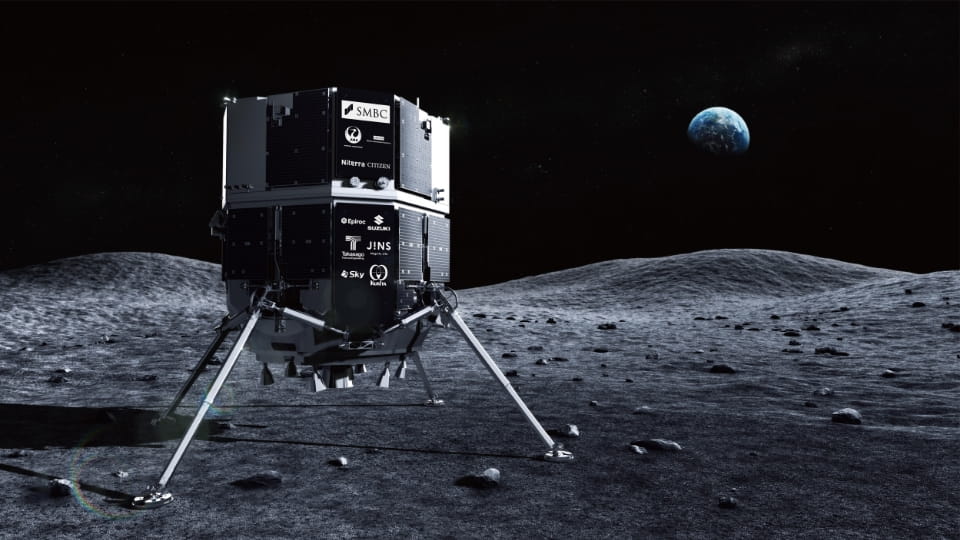
ispace is a lunar exploration company with the vision “Expand our planet. Expand our future.” In 2019, CITIZEN became an ispace corporate partner and began supporting its HAKUTO-R programme by supplying Super Titanium™ for the landing legs of the lunar lander. In 2023, the HAKUTO-R Mission 1 lander secured valuable know-how through an attempted moon landing. In January 2025, Mission 2 launched successfully and is currently en route to the moon. Originally inspired by the romance of space travel, Super Titanium™ is now heading into space for a second time. At CITIZEN, we will never stop exploring and expanding the possibilities of Super Titanium™.
Colour Variations
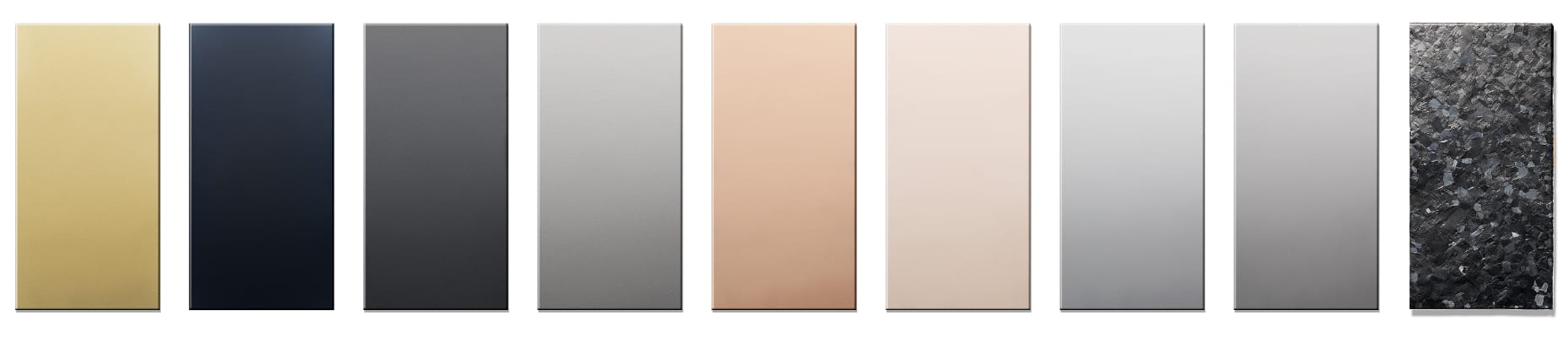
CITIZEN combined sophisticated titanium-processing technology and its proprietary surface-hardening technology DURATECT to transform titanium into advanced Super Titanium™. We have created a rich variety of colours that ordinary titanium cannot express—silver, black, pink gold, sakura pink and the brand-new amber yellow. Thanks to all these colours, we can now make titanium watches that complement a wide range of fashions and styles. The colour variations also reflect the developers’ determination to make watches that set off human skin to best advantage.